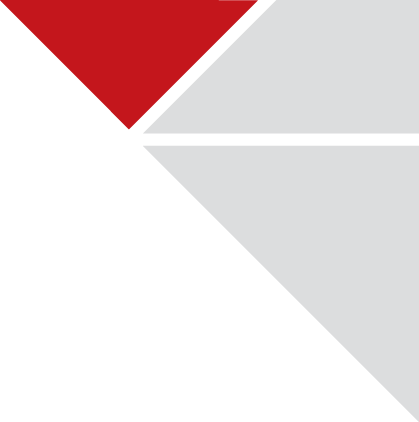
TIPS & TRAINING
Tips and Training by Atkins Framers LTD, U.K.
​
The Morso
These notes can be used as a memory jog after attending one of Atkin Framers Ltd training courses; they should be read in conjunction with the paper written on the Morso blade changing procedure also contained in the course notes. Made in Denmark this precision machine is an integral part of any framers workshop, it is essential for the production of well-constructed frames.
However, as with all machinery it will only perform to its maximum capacity if the framer is fully aware of its functions and is able to put this knowledge to good use.
​
Please remember that Morso blades are hollow ground and extremely sharp, they must never be touched by the operator as serious injury will occur, any debris can be removed using a of piece of wooden moulding.
​
It is essential for a perfect join that blades are kept sharp and chip free, the cost of sharpening is minimal, some grinding companies offer a collection and delivery service with no additional cost.
​
Always keep spare blades in blade box or bolted to a piece of wood for safe storage and transit.
The blades should sit securely on the cast iron head, the part of the machine that moves up and down and in and out, there should be no gaps or over hangs, finger tighten the bolts and make sure the blades are set correctly, tighten each bolt alternately, with a 17mm socket and bar, do not over tighten.
​
As mentioned in the blade changing notes this procedure may take some time and should only be attempted when interruptions are unlikely, cut a test mitre from a medium width scrap piece of moulding, join this test piece with the under pinner, readjust the blade settings if necessary.
​
Also check on a regular basis the bed of the machine, this is where the moulding rests when it is being cut, look at the fences which are locked in place with the stainless steel levers with black knobs, these should be released and moved when the blades are changed, this gives the opportunity for the removal of any accumulation of moulding chips and dust.
​
After cleaning, realign these fences with the factory fitted measuring scale located on the right hand side of the machine; use a steel rule to ensure all three faces are precisely in line with each other.
​
If a second hand Morso has been purchased it is essential that the blades be sent immediately for sharpening, the framer will then know that the blades are correctly ground and sharp.
​
All blades should be inspected regularly to make sure no damage has occurred. Damage to blades however caused will result in an imperfect mitred joint and additional cost from the grinding company.
​
Cutting a perfect mitre is essential part of maintaining a high standard of framing, not only are sharp blades important but the smooth use of the Morso by the framer is also required, this needs practice but one of the major faults is the framer trying to take too big a bite out of the moulding, this can cause the moulding to twist.
​
Do not rely on the rebate supports to keep the moulding square on the cutting bed. Always take several bites even with a narrow moulding; the final cut is used to produce the smoothest finish possible. This will not happen if the blades are blunt or not bolted to the Morso head correctly.
​
It is essential that cleaning and oiling of other moving parts should be carried out on a regular basis. It is not uncommon to see relatively new machines caked with dirt and dust, this can slow down the cutting cycle therefore reducing performance, it can cause the framer to snatch when depressing the foot pedal, also causes fatigue and will result in inaccurate cutting.
​
Look for the oil points on the Morso, lightly oil or grease the moving parts below the blades especially the cam located at the front of the machine located under the lever with the black knob which moves the blade head back and forth. Always use good quality oil, don’t spray with water repellents such as WD40, these products are releasing agents and not lubricants.
​
Complete accuracy should be the goal of all framers, following these simple guidelines will lead to increases confidence and a less stressful workplace, a well maintained Morso used in conjunction with precise mount cutting techniques, also contained in the notes, will help maintain the high standard to which all Framers should aspire.
​
lways be aware of the sharpness of the blades, reasonable precautions will help to reduce the possibility of potentially serious accidents.
​
​
Blade change and various tips
Morso mitring machine has a perfect smooth and accurate cut with double mitre at 45° and single mitre at up to 90°.
​
Safety guard
...Essential as blades are hollow ground and razor sharp,
...When not in use blades should be at furthest in (last cut) position,
...Mitre Gap at base of the mitres rebate supports set too high top of the mitres rebate supports low.
Lubricate
...All moving parts with light oil weekly.
Change Blades
...Each blade is held in position by 3 bolts,
...Remove rebate supports and clean and oil them,
...Using box wrench and bar slacken all bolts by half turn,
...Remove 2 end bolts,
...Slacken centre bolt,
...Turn blade into vertical position, to hold whilst removing centre bolt.
Refit Blades
...Reverse blade changing procedure,
...DO NOT attempt to tighten completely until blades bed together properly with tops level at the front.
Re Sharpen
...Average every 2 months,
...Bolt blades to suitable piece of plywood with bevelled edge outwards when in transit.
Measuring
...Measure rebate size of work to be framed with steel straight edge,
...Allow additional 3mm onto length of each side and for bulky items,
...(oil on stretcher) allow extra 6mm.
...Small section of picture is lost behind frame rebate,
...When it is vital for a particular area to be shown – measure the two dimensions concerned and then cut the moulding to the sight edge.
Cutting Moulding
...Place moulding on Morso machine bed- right hand end under cutting head rebate away from you,
...Adjust rebate supports,
...Cut first mitre hold moulding with hand on either side and several inches away from blades,
...Slide moulding along until the just cut rebate meets graduated mark corresponding to the required length,
...Move sliding stop up to the right hand end of the moulding and tighten the screw holding it in position,
...Bring head down to cut second mitre and at the same time the first mitre of next slide,
...Repeat process to cut other sides.
Tip
-
Cut long sides first:
...Can often be cut down to make a short side if error in measurement or fault exists,
​
-
Wide moulding:
...With lever provided move head back and take small bite,
...Move head forward in steps until cut completed.
Blade Removal
The Morso’s hollow ground blades are the key to good mitre joints, professionally sharpened blades are essential to ensure the mitre is as accurate and as smooth as possible, the machine must be cleaned, oiled and blade settings checked on a regular basis.
Changing the Morso blades takes a little time and patience; it should only be undertaken during a quiet period when there is less chance of interruption. The sharpness and weight of the blades should never be underestimated, a moments’ lack of concentration could result in serious injury.
​
Have the following items close to hand, these items will be needed for the safe removal and replacement of blades, a blade carrying box, screwdriver, block of wood, a 17mm socket and bar, the socket with ‘T’ bar supplied by Morso can also be used to release the bolts.
​
The socket and ‘T’ bar should be used to lock down the cutting head when the machine is not is use.
Push the cutting head, on which the blades are bolted, to the back of the machine, the rebate supports can either be removed or positioned to ensure sufficient access to the bolts holding the blades.
​
If there is only one carrying box, remove the newly ground blades, placing them safely on an easily accessible secure surface.
​
Place the wooden block under the blades, this will stop the blades dropping when the last bolt is removed, release the top and bottom bolts and insert the screwdriver into the hole left by the top bolt, remove the centre bolt. As the blade is supported by the wooden block and the screwdriver the operative should be able to remove the screwdriver and carefully slide the blade off the cutting head and place in the carrying box.
​
Repeat this procedure for the remaining blade, please note, over the years it has become apparent that some framers do not have the strength in their fingers to support the blade whilst the last bolt is being removed. This can cause the blade to slip from the cutting head down into the machine; this not only damages the blades but is potentially very dangerous. Therefore the use of the block of wood and screwdriver is recommended.
​
If the blades do slip away from the operative during the blade changing cycle – DO NOT try and catch them, step back and let them fall, better a damaged blade than a badly cut hand or the loss of a finger of thumb.
Reverse this procedure to fit the newly sharpened blades, remember to support the blades with the wooden black and the screwdriver through the top hole until the centre bolt is in place.
​
The blades, which should always be hollow ground, if sharpened with a purpose built grinding machine, are both sharpened at the same time, when refitting to the Morso they should fit perfectly. Only finger tighten the blades until they are perfectly aligned, use a piece of wood or the wooden handle of a hammer to gently tap the blades into place before the final tightening.
​
Do not over tighten the bolts, it may take a little time to get the hang of aligning the blades properly, persevere, the perfect mitre is worth the effort.